Short thesis on the manufacturing of custom productsÂ
Our production process has changed a lot year in the past 5 years. At Merit making custom products is at the heart of everything we do. The biggest challenge we face making custom products is that every fabric pattern is different, which makes standardizing and batching manufacturing processes difficult. But the process of sewing the bags together is always the same. Making custom frame bags for bikepacking is a very niche part of the cycling industry, the reason why there are so many small makers is due to the non-scalability of making custom products. In the beginning, we spend around 7 hours average per custom frame bag, which is not sustainable for manufacturing bussiness, but at Merit, we believe it is possible to scale the production.Â
The main goal of Merit is to try to make “Custom the new standard”.
Current Manufacturing Process
Process innovation in the custom gear industry is quite sparse. Some small makers are still using the tracing over cardboard technique to communicate their internal bike frame dimensions. This has a lot of downsides like having to send the cardboard template to the maker, human mistakes and interpretation, and more cost. Currently, most companies work with a photo of the frame with a measuring tape, which they use to calibrate and scale the picture to obtain the correct dimensions. This technique is a 2D form of Photogrammetry or CAD design. With these dimensions the makers still needs to design the patterns, draft or print physical patterns on paper, trace them on the fabric, and cut them out by hand. This four step process or something similar is currently the main strategy for most makers.
In the video below, Mickey demonstrates how a Frame Bag is made in the old fashioned way.
Merit’s Manufacturing Strategy and development
- Patch 1.2022 “Nesting Algorithm and Lasercutting”
We developed a process that simplifies this four step process in one and also enables a smoother transition to the sewing phase. Most of the design and pattern drafting happens behind the computer (CAD), and is “currently” still done by Mickey. But instead of making physical patterns and laying them out on the fabric, these parts are converted into vector files and put into a Nesting Algorithm. This algorithm sorts all the parts onto a fabric sheet as efficiently as possible, reducing waste, production time, and strain on the maker. Afterwards, the cutting files get inserted in a lasercutting machine, that is able to cut the fabric very fast and melts the edges to prevent them from fraying.
Patch 2.2023 “Lasermarking for part distinction”
This Nesting process is great, but there are several problems as well. For example, it works great when you have to make one full black Frame Bag, but what happens when you need to make 10 black frame bags that consists of only unique but similar shaped parts? One frame bag consists roughly of 30 unique parts, which results in 10*30 = 300 unique parts! (this of course scales linearly with quantity) . It becomes an organizational nightmare. To remedy this, we have programmed our own algorithm that lasercuts an unique number in the seam allowance of the parts (the material that dissapears in the seams) for every part of the bag. This solves the division of parts after lasercutting, again reducing production time and strain on the maker.
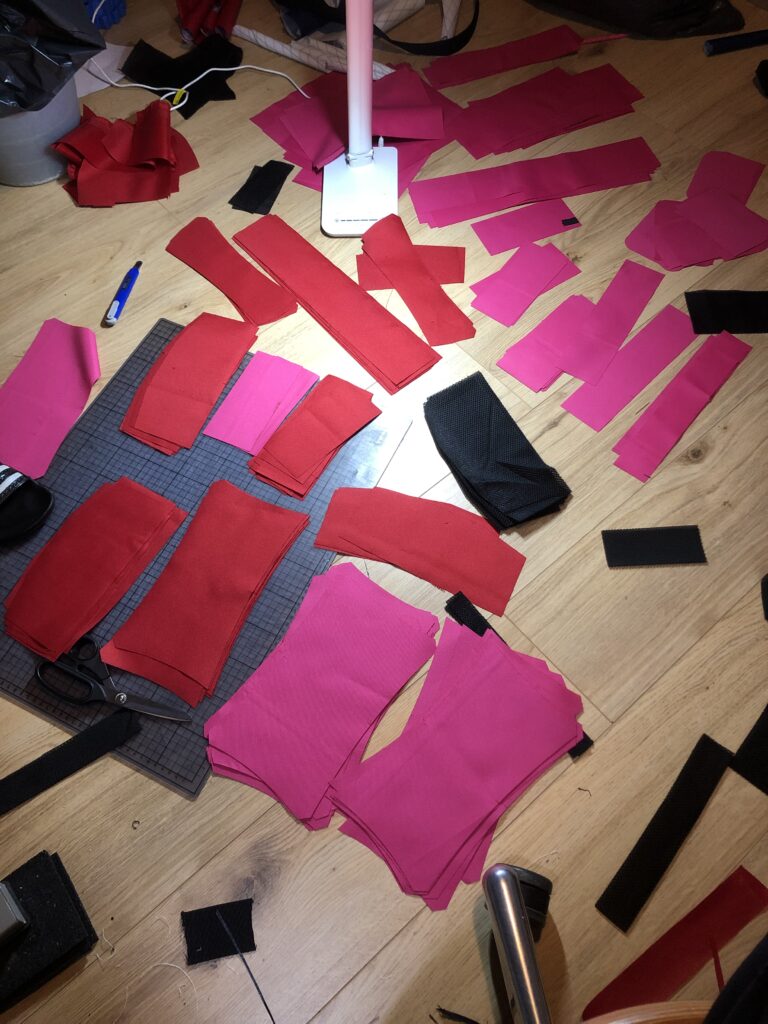
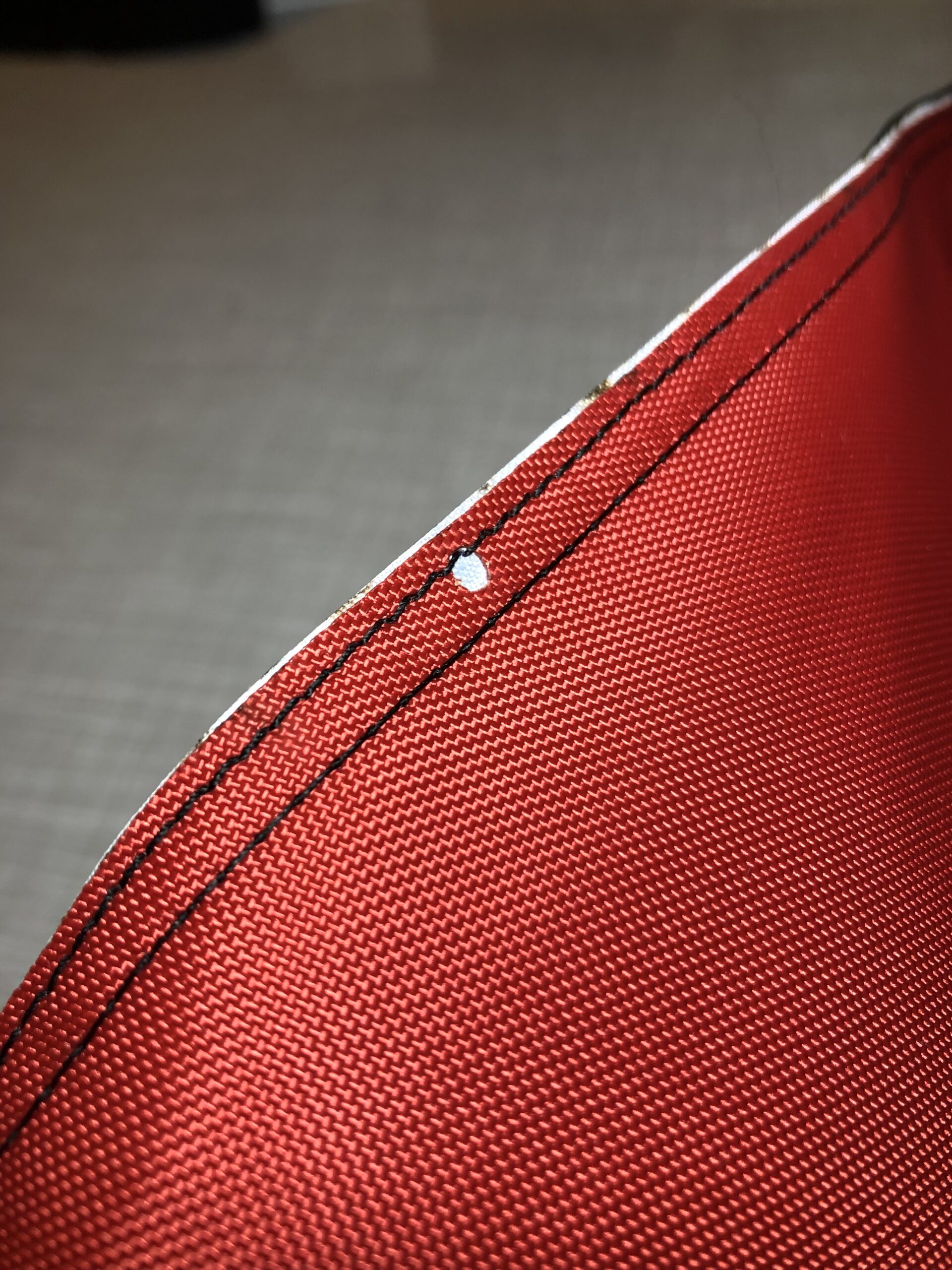
- Patch 3.2023 “Application of sewing guide lines on parts”
But of course, we can apply this lasercut marking technique in the seam allowance for other things as well. During the design process, the bag also need components like straps, zippers, et cetera. All the positions of the components are fully defined during the CAD Design Phase and during the Sewing Phase all the components need to be sewn in position. Currently, this is done by marking all the positions with chalk and then attaching the corresponding component (a 2-step process). We can reduce this to one step by marking the component positions in the seam allowance during the lasercutting phase. Allowing the sewing machine operator to recognize what to sew and where during assembly. This is like having instructions etched onto the parts, again reducing time and strain on the makers.
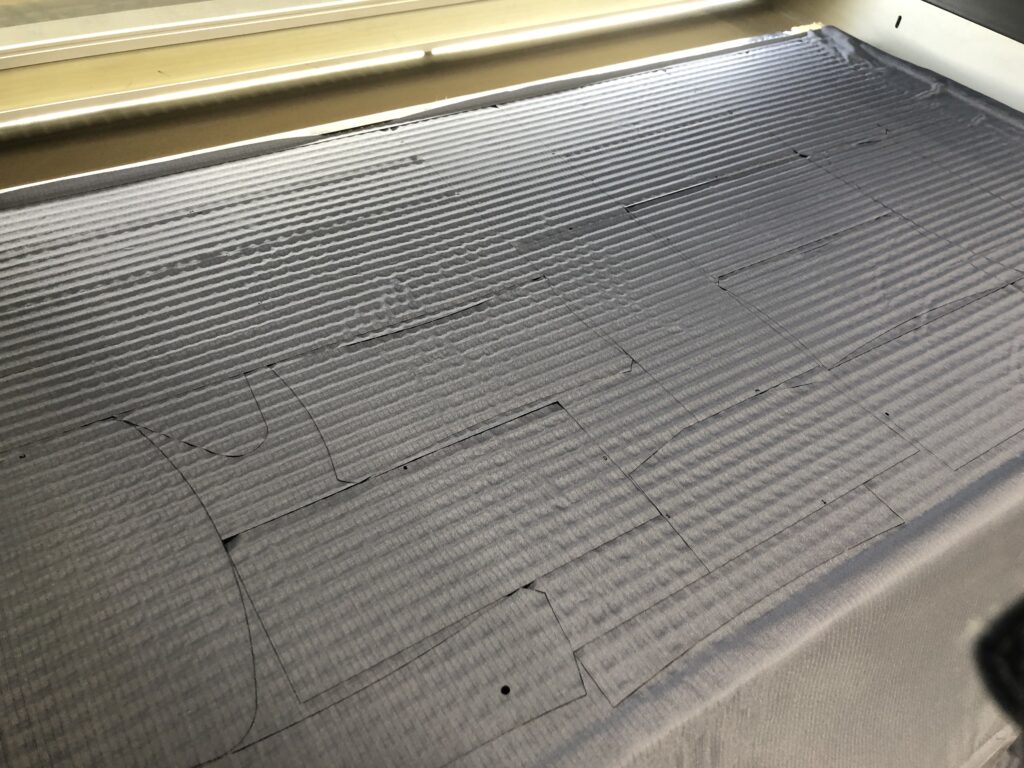
- Patch 4.2024 “More to come”
Some previews…
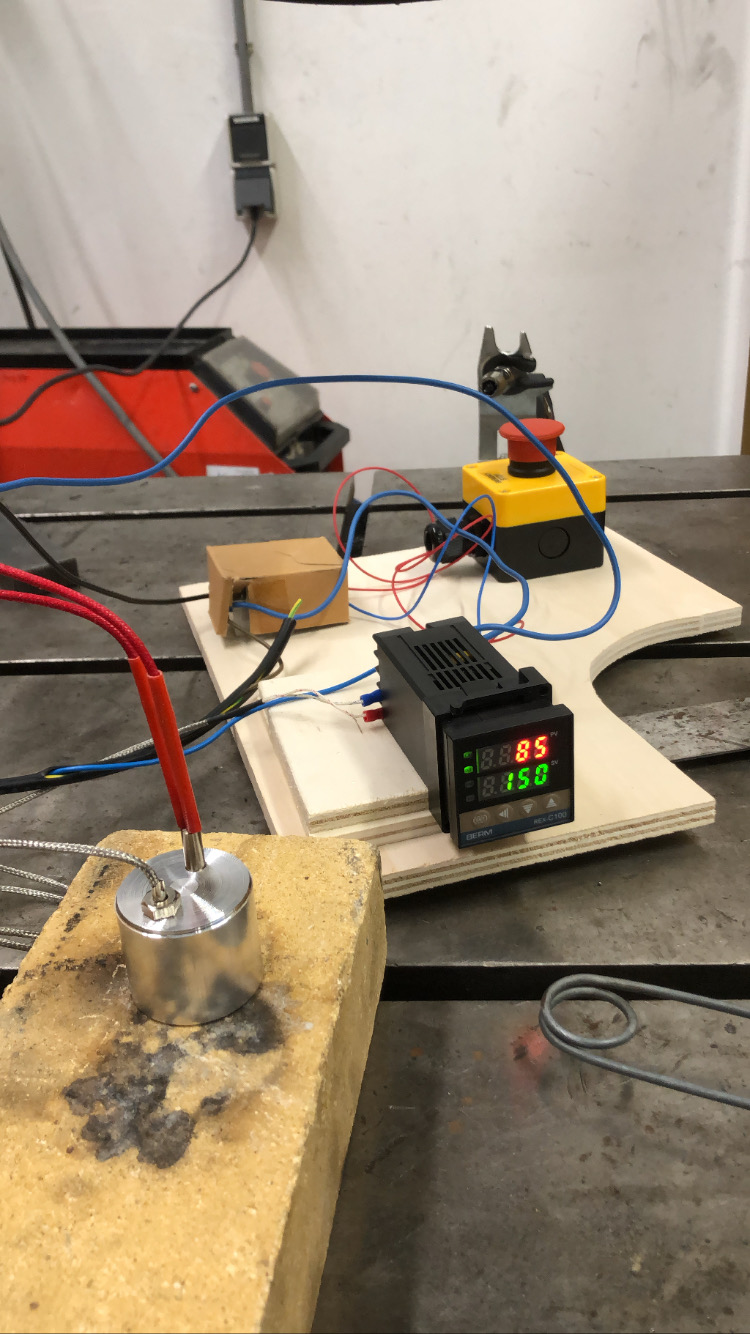
“It’s not about Bikepacking bags, it never was”
At Merit, our goal is to try to make “Custom the new standard”. This does not only apply to our Bikepacking products, but this ethos is implemented in all of our research and development in the field of design, production, and customer interaction.
- Generation of Tailored Made Clothing patterns
To be written…
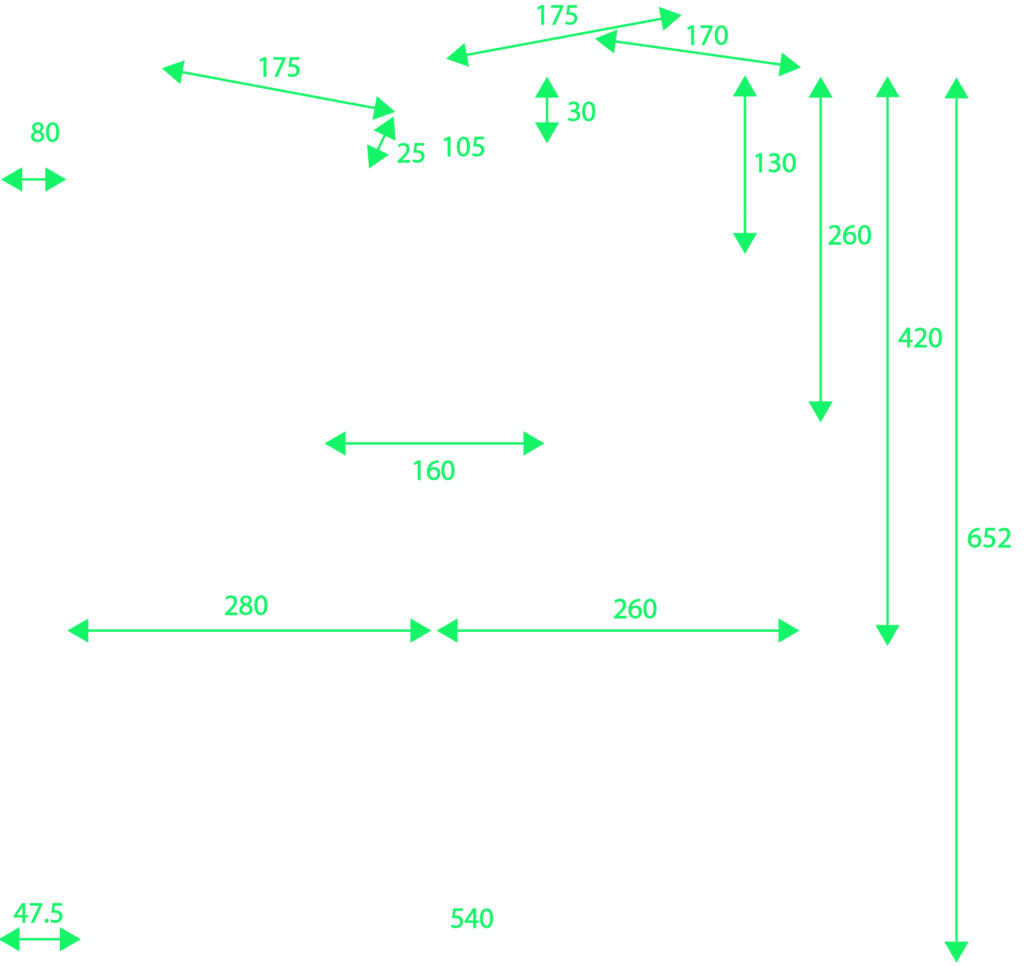
Tailor fitted Ski Clothing 3-2-2024
For my first skiing trip, I decided to set the goal of making my own ski jacket, pants, and sport backpack. I designed the jacket with multi use in mind, so I could use the jacket for daily life. The style is similar to the sewing jacket (I do like the rugged workshop style). For clothes, I generally like to keep the materials as organic as possible. That’s the reason I used cotton canvas as the main fabric, which I waxed with beeswax to make it as naturally waterproof as possible. The inside has been lined with a layer of wool for insulation. The waterproofness of beeswax decayed over time due to me tumbling from the ski slope. The waxed canvas was entirely unharmed by the abrasion of ice and snow. A lot of takeaways from this experience for future developments!
- Custom Tailored BackpackÂ
To be written…
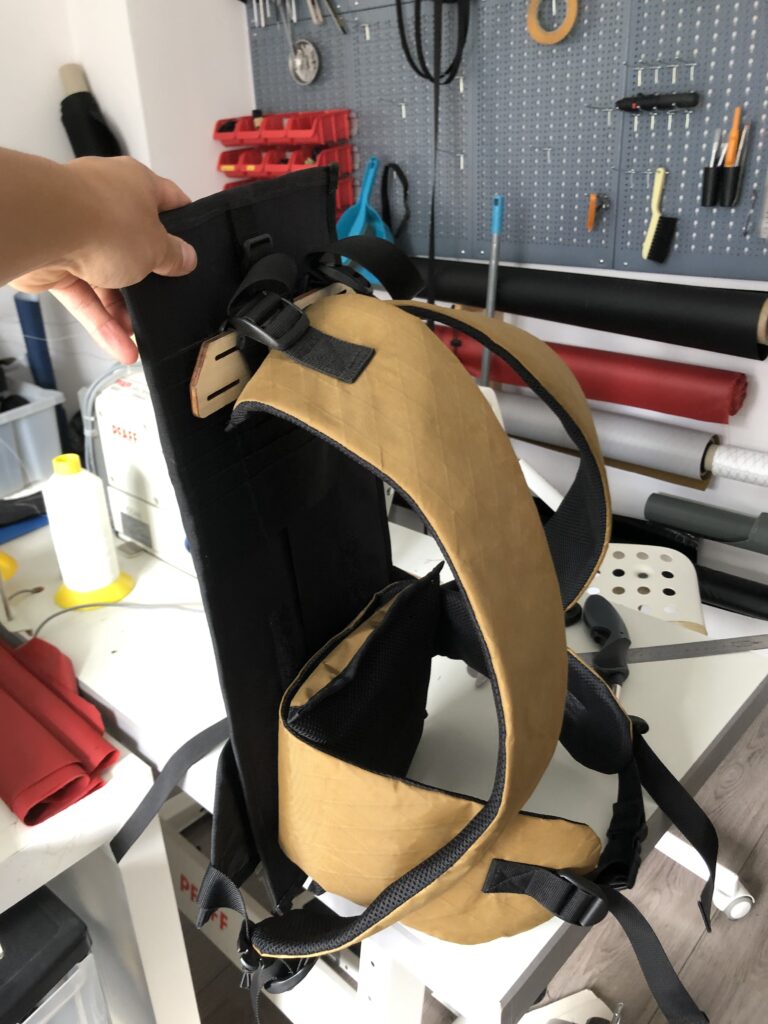
- Custom Trekking tent in collaboration with
Wytze de Vries
To be written…
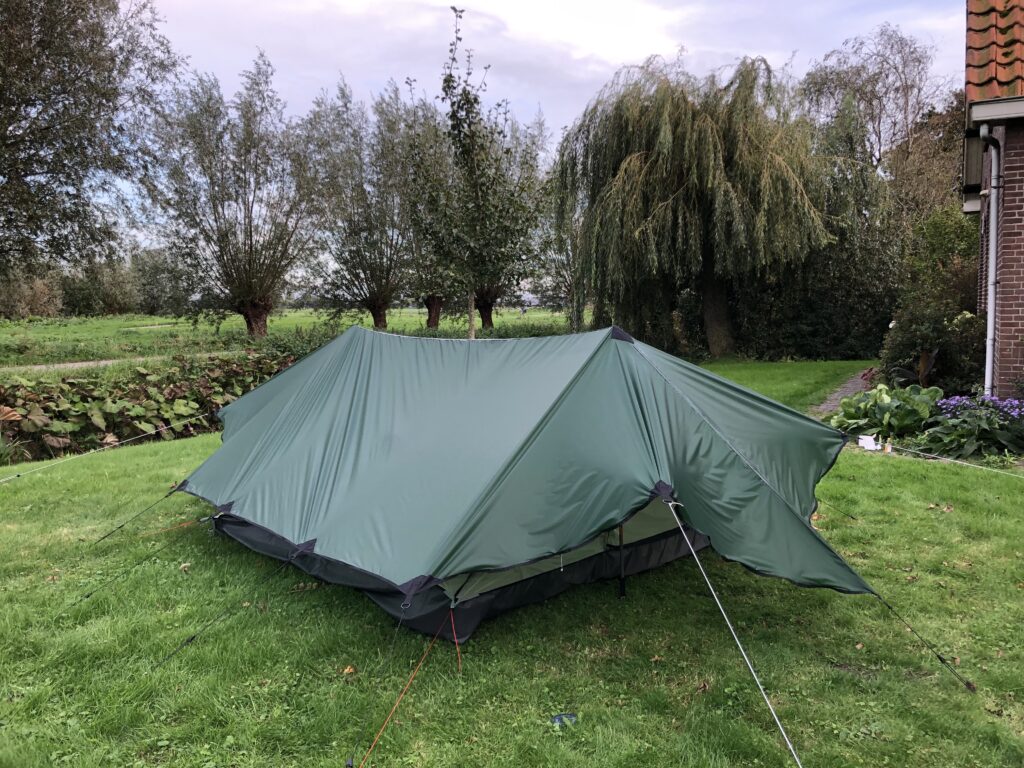
- Looking further than only textiles
To be written…
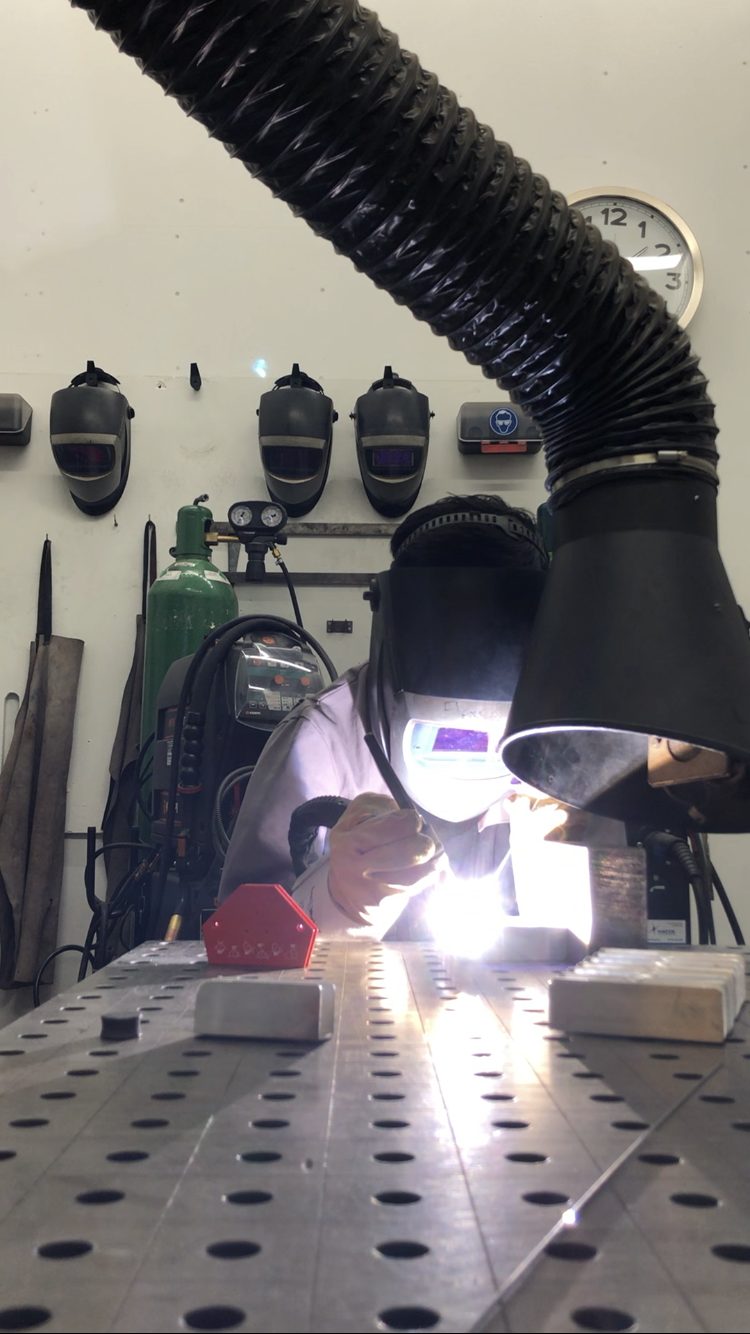